![]() |
FESTO SMARTBIRD |
A
German company called 'Festo
corporate',
have made a robotic bird which is inspired from the herring gull. The
flying model impresses with its outstanding aerodynamics and maximum
agility and is able to take off, fly and land without an additional
drive.
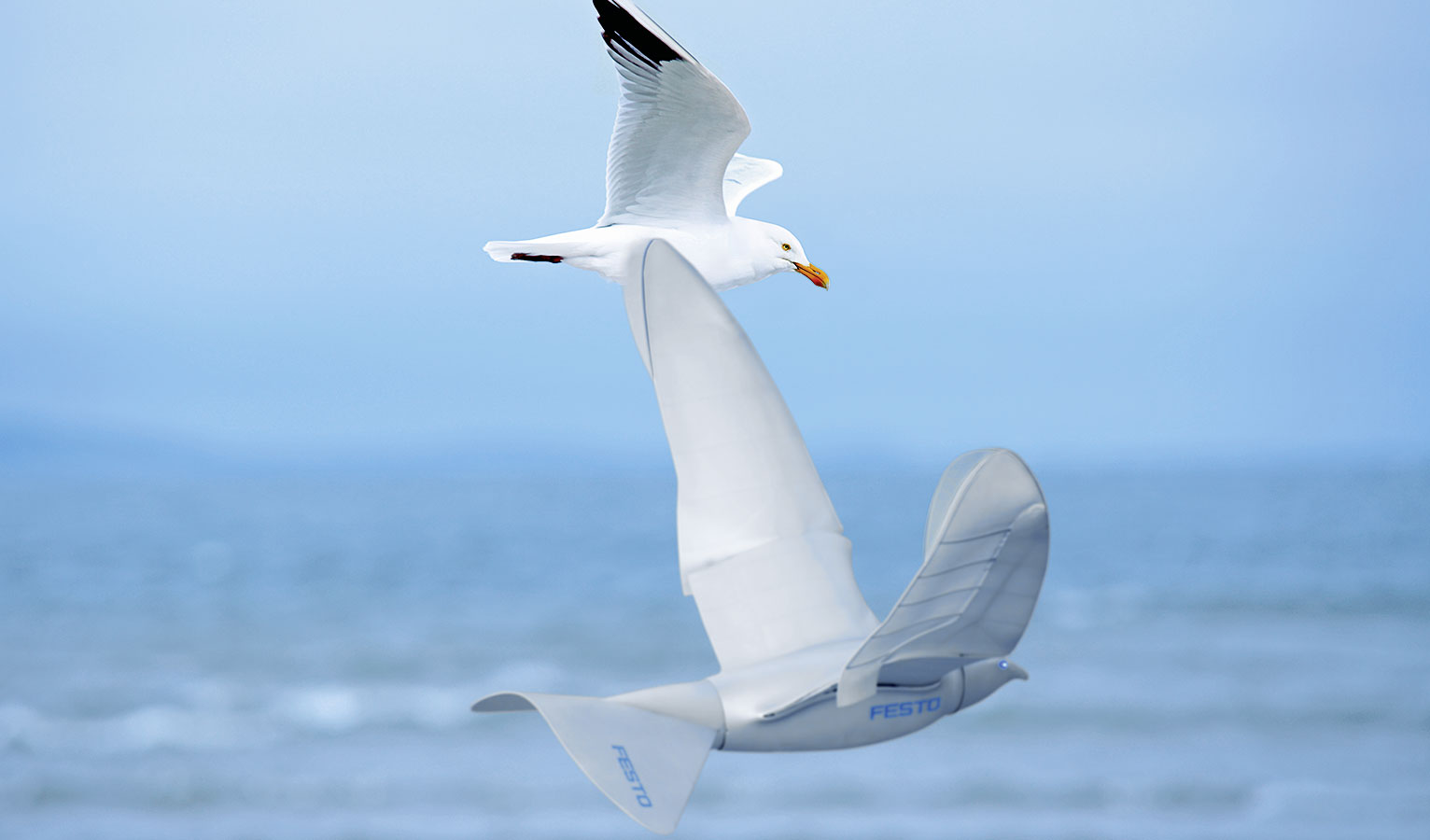
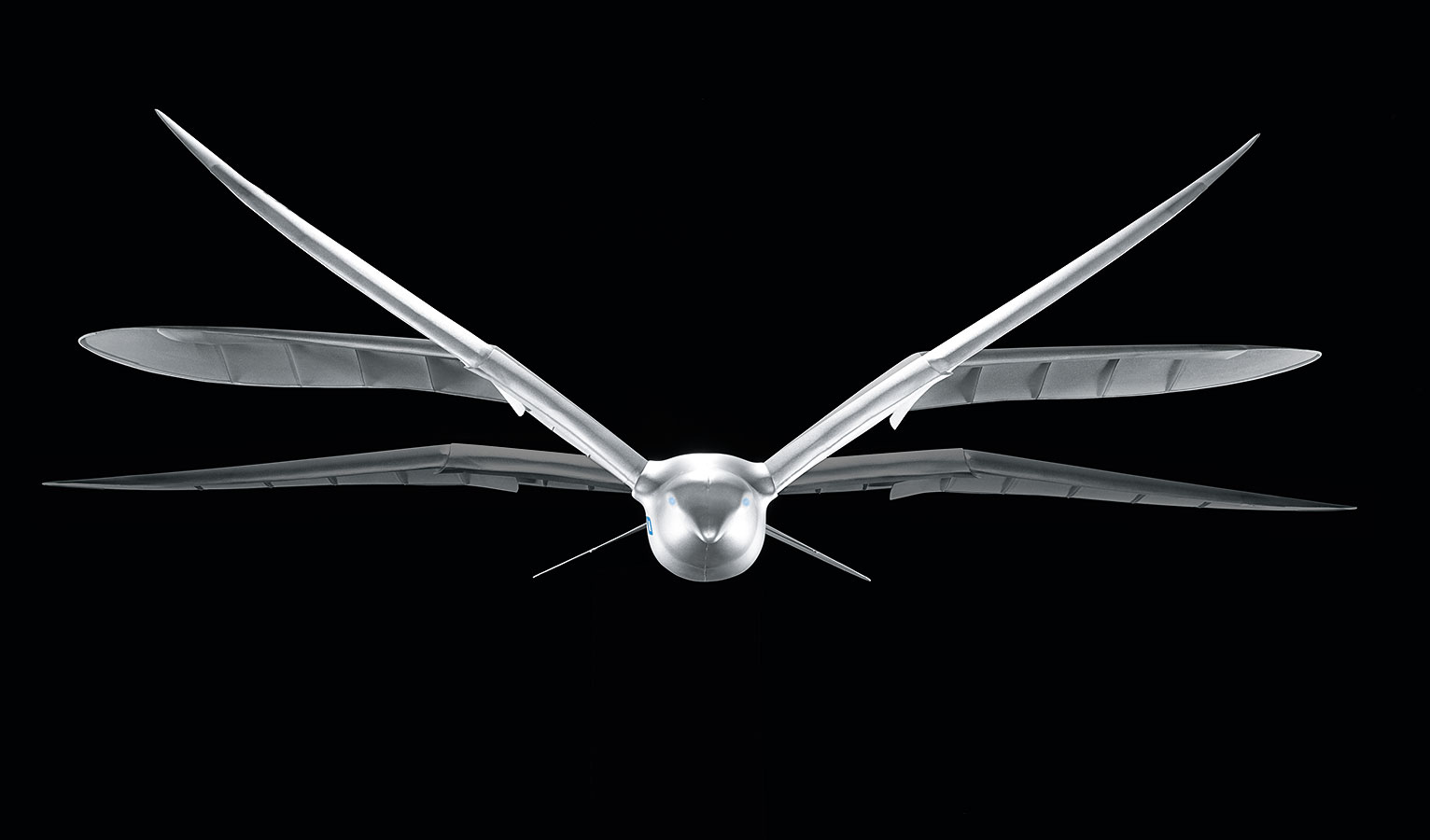
Smart-Bird’s wings each consist of a two-part arm wing spar with an axle bearing located on the torso, a trapezoidal joint as is used in enlarged form on industrial excavators, and a hand wing spar. The trapezoidal joint has an amplitude ratio of 1:3. The arm wing generates lift, and the hand wing beyond the trapezoidal joint provides propulsion. Both the spars of the inner and the outer wing are torsional resistant. The active torsion is achieved by a servomotor at the end of the outer wing which twists the wing against the spar via the outmost rib of the wing.
The torso: a secure housing for the technology
The battery, engine and transmission, the crank mechanism and the control and regulation electronics are housed in Smart-Bird’s torso. By means of a two-stage helical transmission, the exterior rotor motor causes the wings to beat up and down with a reduction ratio of 1:45. This motor is fitted with three Hall sensors that precisely register the wing’s position. Both the flapping and bending forces are conveyed from the transmission to the hand wing via a flexible link. The crank mechanism has no dead center and thus runs evenly with minimal peak loads, thus ensuring smooth flight. The opposing movement of the head and torso sections in any Spatial direction is synchronized by means of two electric motors and cables. The torso thus bends aerodynamically, with simultaneous weight displacement; this makes Smart-Bird highly agile and maneuverable.
The tail section: an aid for lift and control
The tail of Smart-Bird also produces lift; it functions as both a pitch-elevator and a yaw rudder. When the bird flies in a straight line, the V-position of its two flapping wings stabilizes it in a similar way to a conventional vertical stabilizer of an aircraft. To initiate a turn to the left or right, the tail is tilted: when it is rotated about the longitudinal axis, a yaw moment about the vertical axis is produced.
the dynamics of the bird that matter
Propulsion and lift are achieved solely by the flapping of the wings and have a power requirement of only 25 watts. Smart-Bird has a total weight of around 400 grams and a wingspan of 2 meters. It is thus an excellent example of functional integration and resource-efficient extreme lightweight design, and demonstrates the optimal use of airflow phenomena. The control of the time behavior of wing bending and wing torsion takes place within the tact of a few milliseconds and results in optimum airflow around the wings. The Smart-Bird flight model has no rotating parts on its exterior and therefore cannot cause injury.
Functional integration for hybrid technology
This function integration provides information for the development and optimization of hybrid drive technologies. With the hybrid axis, Festo is already combining the advantages of pneumatics with those of electric linear axes to achieve rapid, high-precision linear actuator technology.
Possible fields of application
The applications of coupled drives for linear and rotary movement range from generators that derive energy from water so called stroke wing generators to new actuators in process automation.
REFERENCES:
0 Comments